1 단조(forging)
잉고트(ingot)의 소재를 단조 기계나 해머로 두들겨서 성형하는 가공법으로 자유 단조와 형 단조로 구분한다.
1) 형별 구분
- 자유단주 : "해머, 수공구를 이용하여 가공업셋팅, 늘이기, 단짓기, 굽히기, 구멍뚫기"
- 형단조 : 프레스를 통한 단조
2) 온도별 구분
- 열단단조 : 해머단조, 프레스단조, 업셋단조, 압연단조
- 냉간단조 : 콜드헤딩(볼트, 리벳헤드), 코이닝, 스웨이징
2 압연, 인발, 압출, 전조
1) 압연(rolling) : 회전하는 두개의 롤러 사이에 제품을 통과시켜 두께 폭을 조절
금속 재료를 회전하는 롤러 사이에 통과시켜 성형하는 방법으로 판의 제조에 이용되며, 봉(bar), 관(pipe), 형강재, 레일 등도 만들 수 있다.
2) 인발(drawing) : 딥드로잉 이음매가 없는 용기 제작에 사용됨
다이(die)의 구멍을 통하여 재료를 축방향으로 당기어 바깥 지름을 감소시키는 가공법으로 봉, 관, 선의 제조에 이용된다.
3) 압출(extruding) :
금속을 실런더 모양의 컨테이너에 넣고 한쪽에 램(ram)에 압력을 가하여 밀어내어 가공하는 방법으로 봉, 관, 형재의 제조에 적용한다.
- 직접압출
* 램, 소재가 같은 방향으로 이동
* 소재가 20~30% 남음(재료손실)
* 마찰저항이 크다(동력소모가 많다)
- 간접압출
* 램, 소재가이동방향이 반대
* 재료손실이 직접압출대비 적다
* 마찰저항이 적다(동력소모가 적다)"
- 충격압출
* 펀치로 재료를 순간적으로 압착하는 방식
* 두께가 얇은 원통형상 제품을 성형함(화장품케이스등)
- 제관
* 천공법
* 만네스맨법 : 속이 찬 봉재를 길이방향으로 이음매없는 관을 제조
* 스티펄법
* 에르하르트법
4) 전조
- 마주보는 한쌍의 다이, 롤러 사이에 원통형 소재를 넣고 회전시켜서 표면을 가공
- 나사 기어 스플라인등을 가공
- 절삭가공에 비해 표면이 매끄럽고 압축잔류응력으로 표면경화 가능.
3 프레스 가공
판재를 펀치(punch)와 다이(die) 사이에서 압축하여 성형하는 방법이며, 전단 가공, 굽힘, 압축, 딥 드로잉(deep drawing) 등으로 분류한다.
1) 종류
- 컷팅(cutting)
- 펀칭(피어싱)
* 구멍을 만드는 가공
* 소재에서 원형이 제거된것이 제품
- 블랭킹(blanking) : 원형 제품을 따내는 가공, 원형 자체가 제품
- 전단 : 원소재를 자르는 가공
- 트리밍 : 일정한형태(일반적으로 원형)으로 절단하는 가공
- 셰이빙 : 각진부분을 다듬는 가공
- 노칭(notching) : 제품의 모서리에 여러형의 노치를 만드는 것(제품일부를 떼어내는 가공)
- 셰어(shear) : 제품을 나눔
- 세퍼레이팅(seperating) : 2개 이상의 반완성품을 잘라내는 가공
2) 모식도
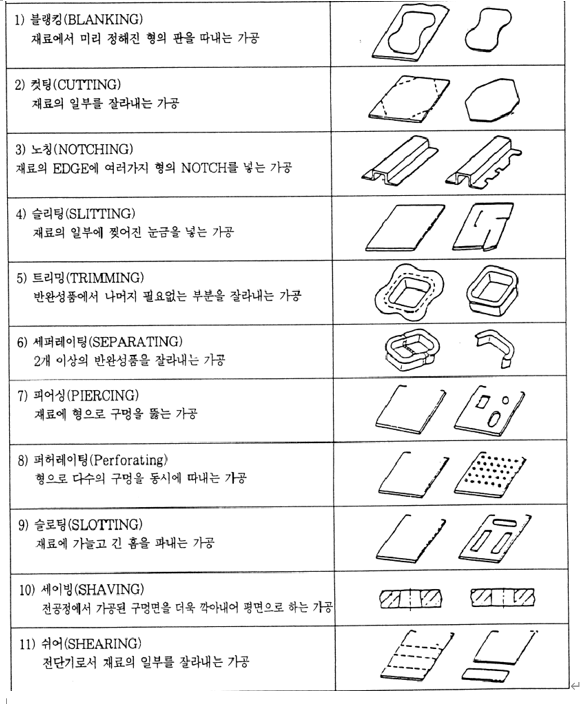
4 성형
1) 개념 : 설비공구를 이용하여 제품을 목적에 맞게 형상을 만들어내는 가공
2) 종류
- 스피닝 : 보올(bowl)형태의 제품을 성형
- 시밍 : 두개의 소재를 구부려서 연결하는 가공법
- 컬링 : 제품끝단을 말아서 둥글게 만드는 가공법
- 벌징 : 원통형 재료 일부를 볼록 나오게 만드는 가공법
- 비딩 : 회전하는 졸러 사이에 소재를 넣어서 홈을 만드는 가공법
- 마폼법 : 다이대신 고무를 이용하여 제품을 성형하는 가공법
- 하이드로폼 : 마폼법에서 액체에 압력을 가하여 성형하는 가공법
- 코이닝
* 상형/하형 두개의 다이 사이에 소재를 넣어서 표면에 형상을 만드는 가공법
* 소재의 두깨변화가 없는 수준으로 표면에 형태를 만듦
- 엠보싱 : 상형/하형 두개의 다이 사이에 소재를 넣어서 요철을 만듦
- 스웨이징 : 막대 튜브형상 재료의 단면을 축소시키는 가공
대분류
|
중분류
|
소분류
|
특징
|
그림
|
●단조
(Forging)
두들겨서
|
(방법에 따라)
|
자유단조
|
*해머, 손공구 등을 이용
*업셋팅, 늘이기, 단짓기, 굽히기, 구멍뚫기 등
|
|
형단조
|
*프레스를 이용
(치수정확. 대량생산 가능)
|
|
||
(온도에따라)
→ 기준 :
★재결정온도
|
열간단조
|
해머단조, 프레스단조, 업셋단조, 압연단조
|
|
|
냉간단조
|
콜드헤딩 (볼트, 리벳머리 만드는거 생각)
코이닝, 스웨이징
|
|
||
●압연
Rolling
|
두 롤러사이에 제품이 통과 → 두께, 폭, 직경 축소
|
|
||
●인발
Drawing
|
롤러를 사용하지 않는다 (축방향통과)
외경을 줄이는 가공법
|
|
||
|
딥드로잉
|
*이음매가 없고 바닥있는 용기 제작 (음료용 캔, 싱크대 등)
(참고로 두께가 균일하게 가공되진 않는다)
(포스팅 맨아래 보충설명)
|
|
|
●압출
Extruding
|
★단면이 균일한★ 긴 봉, 관 등을 만드는 가공법
|
|
||
(압출
방법에 따라)
|
직접압출
|
*램, 소재가 같은방향으로 이동
*소재(압출재)가 20~30% 남는다 (=재료손실)
*마찰저항이 크다 = 동력소모가 많다
|
|
|
간접압출
|
*램, 소재이동방향이 반대
*재료손실이 적다
*마찰저항이 적다 = 동력소모가 적다
*표면상태 별로, 조작 불편함
|
|
||
충격압출
|
*주로 제품두께가 얇은 원통형상
*치약튜브, 화장품케이스 등
|
|
||
●제관
Pipe
Making
|
관을 만드는 가공법
|
|
||
천공법
|
만네스맨법
|
속이찬 봉재를 길이방향으로 이음매없는 강관제조
|
앞글자만 따서 외워놓기
만스에충 (발음이 만세충과 비슷...)
|
|
스티펄법
|
만네스맨법과 비슷. 파이프 지름확대
|
|||
에르하르트법
|
|
|||
충격압출
|
|
|||
●전조
Form
Rolling
|
* 다이, 롤러사이에 소재를 넣은 후 회전(이동)시키며 가공
- 나사, 기어, 볼, 스플라인축 등 가공
* 매끄러운 표면 얻음. 소재 표면에 압축잔류응력 → 피로수명 ↑
|
|
||
●프레스
Press
|
전단
|
펀칭
(피어싱)
|
* 말그대로 구멍뚫는것
* 종이 펀칭기 생각해보자. 우린 구멍이 뚫린 종이를 사용함 (뚫린 동그란 종이부분은 버림) → 남은쪽이 제품
|
|
블랭킹
|
* 펀칭과 반대. 제품을 따내는 가공
* 뚫은 부분이 제품, 남은 부분은 버림
|
|
||
전단
|
*절단하는 작업
|
|
||
트리밍
|
*둥글게 자름
|
|
||
셰이빙
|
*각진 부분을 다듬질
|
|
||
노칭
|
*제품 일부를 따내는 작업 (제품에 노치를 줌)
|
|
||
분단
|
*제품을 나누는 과정
|
|
||
성형
|
스피닝
|
*국그릇 모양의 몸체가공. 원통 외엔 가공못함
|
|
|
시밍
|
*구부려서 연결
|
|
||
컬링
|
*끝 말아서 테두리를 둥글게
|
|
||
벌징
|
*원통형 재료 일부를 볼록 나오게
|
|
||
비딩
|
*회전하는 롤러 사이에 소재 넣어서 홈 만듬
|
|
||
마폼법
|
*고무를 다이대신 이용
|
|
||
하이드로폼법
|
*마폼법과 같이 다이대신 고무를 이용하고, 고무 안에 액체를 넣어 강한압력 줌
*다소 복잡한 모양을 성형. hydro=액체 떠올리기
|
|
||
굽힘가공
|
가공 후 스프링백 발생 (철사 접고 손 뗐을 때 일부 탄성복원 되는 현상 생각)
|
|
||
압축
|
코이닝
(압인가공)
|
*coining → coin → 동전생각 (앞뒤 모양 다름)
*상,하형이 서로 다른 (관계없는) 요철
*소재의 두께 변화가 있음
|
|
|
엠보싱
|
*요철 가공하는 방법
*엠보싱 휴지 생각해보기 → 상하형이 서로반대
*소재의 두께변화가 없음 (상하형 서로 반대형상이니까)
|
|
||
스웨이징
|
*막대, 튜브형상 재료의 단면을 축소시키는 가공
(다이의 왕복운동 등을 이용)
|
|
딥드로잉
드로잉 자체는 이음매가 없으면서 밑바닥이 있는 용기를 만드는 공법이며, 여기서 deep 이란 용기의 깊이가 직경 대비 상대적으로 깊다는 의미입니다.
세번째 그림과 같이 블랭크홀더가 재료부분을 좀 잡고 있으면 가장 아래의 오른쪽 제품처럼 가공이 될 것이고,
펀치가 재료를 끝까지 다 밀어넣으면 왼쪽같이 가공이 될 것입니다.
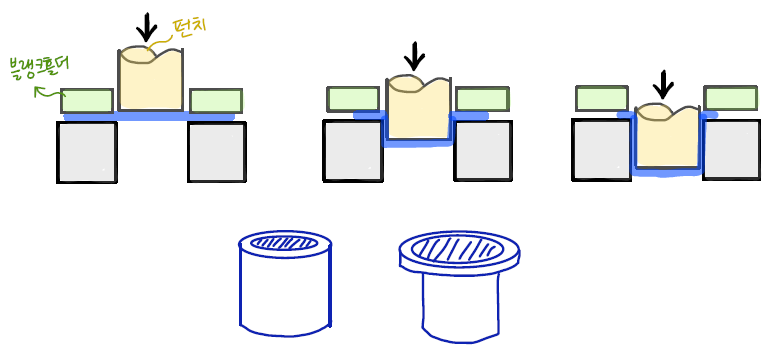
'건축자재 > 알루미늄 압출' 카테고리의 다른 글
알루미늄 제품설계 제작 도장 가공 (0) | 2023.05.17 |
---|---|
압출 (0) | 2023.03.26 |
알루미늄 압출성 (3) | 2023.03.14 |
알루미늄 방열판 히트싱크 heat sink (0) | 2023.03.14 |
알루미늄 주문제작 설계 생산 (0) | 2023.02.11 |